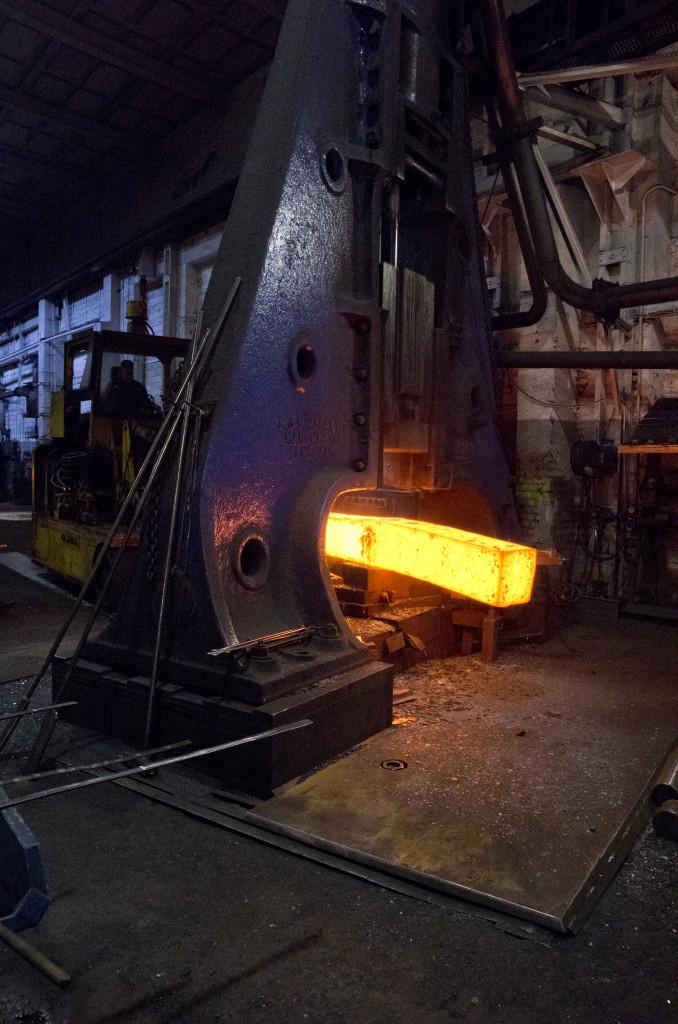
I en hammarsmedja med anor från 1600-talet formas järnet på traditionellt vis till gafflar för de verkligt stora truckarna. Men Scana i Värmland kan mer än så.
Den norska koncernen Scana etablerade sig på 1990-talet i Värmland när man köpte Bofors smidesverksamhet i Karlskoga och samtidigt blev ägare till järnverket i Björneborg, några mil söderut.
Företaget med den stora hammarsmedjan fick namnet Scana Booforge, för att återkoppla till Bofors traditionsrika namn. Vid Booforsen, som skulle ge Bofors sitt namn, låg en smedja redan 1646. När aktiviteterna på 1970-talet var på sin höjdpunkt på det stora industriområdet arbetade här 10 000 personer. Men sedan dess har den gamla försvarsindustrin fått se om sitt hus åtskilliga gånger, och mycket har hänt.
Idag arbetar Booforge tillsammans med Scana Machining i Kristinehamn, stålverken i Björneborg och Söderfors samt ingenjörsfirman Subsea mot kunder inom bland annat maskineri, energi, försvar och offshore, alltså olje- och gasindustrin (se faktaruta). Vi ska återkomma till Scana Machining om en liten stund.
På Scana Booforge har man valt att kliva uppåt i näringskedjan och erbjuda förädlade produkter och kvalificerade tjänster. Ett exempel är tillverkningen av gafflar för truckar som förändrats under de senare åren.
Henrik Fintling är marknadschef på Scana Booforge, och han kan berätta mer:
– Vi har gjort gafflar sedan 1950-talet. Till en början levererade vi dem som blanka ämnen, men vid millennieskiftet började vi svetsa kompletta gafflar, och vi tillverkar också master och gaffelvagnar som gafflarna sitter på. Förädlingen har lett till att denna försäljning idag står för cirka 60 % av vår omsättning, och det är en fördubbling jämfört med tidigare.
– Här jobbar vi med friformssmide som innebär att man i stor skala smider som man alltid gjort i smedjor: man hettar upp materialet och bearbetar det med en hammare.
En 4-tons hammare lyfts med tryckluft, och faller ner på materialet tills det fått önskad form. Det upp till 3 ton tunga, gulvitglödgade materialet kan vara upp till 475 x 475 mm i profil, och har en temperatur på 1 000 grader. När hammaren har arbetat färdigt är profilen klar att formas till en gaffel. Det är ett utpräglat hantverk, och att bearbeta den glödande klumpen till en gaffel eller ett kanonrör kräver kunnande och erfarenhet.
Det är ovanligt med friformsmide idag, för de flesta hammarsmedjor försvann redan i mitten av 1900-talet. Nu dominerar metoder där materialet pressas (smidespress) eller slås ut i en form (sänksmide).
– Men det finns kvalitetsmässiga fördelar med friform – du kommer närmare i mått och får en jämnare yta jämfört med pressmide, om du inte använder speciella verktyg, förklarar Henrik. Friform passar bra till gafflar och andra småvolymprodukter i höglegerat stål.
När gaffeln fått sin form och bockats till ett ”L” ska den värmebehandlas för att få rätt specifikation på stålet.
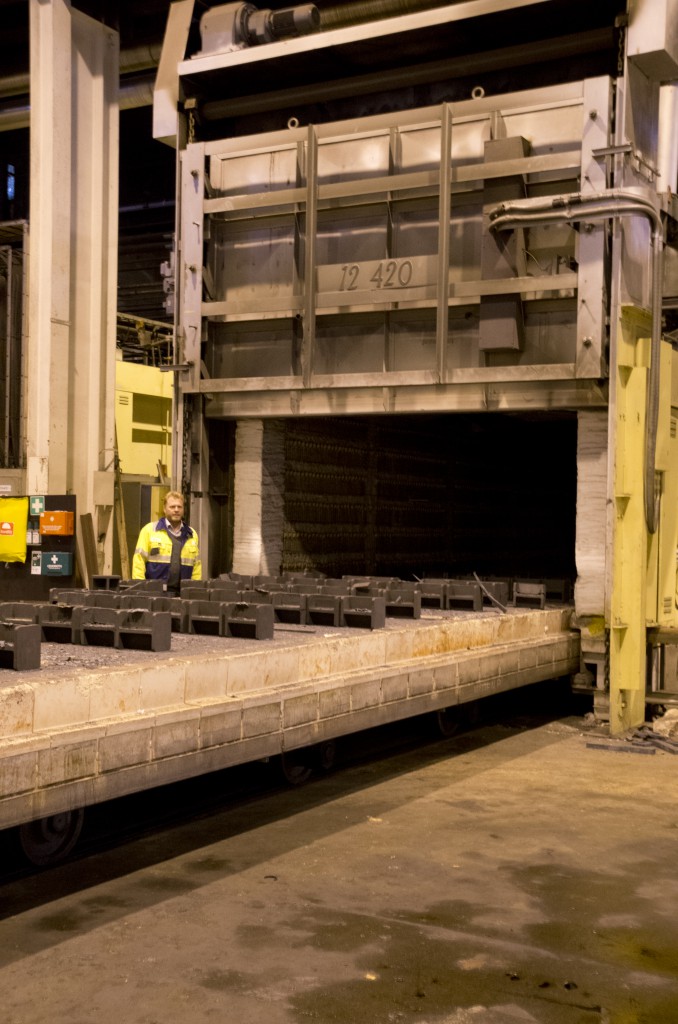
Vad är då poängen med värmebehandling? Flera, visar det sig.
En enkel användning är att eliminera inbyggda spänningar i svetskonstruktioner, en annan att normalisera materialet, alltså att få tillbaka en jämn struktur i hela godset. För produkter som gafflarna gäller det i första hand att öka sträckgränsen genom seghärdning och att genom anlöpning få en hård yta över den sega kärnan.
Värmebehandlingen är en kritisk del av processen. Ett ståls hela potential kan tas fram med en värmebehandling som är anpassad efter användningsområdet. Man kan också återställa ett stål efter olika behandlingar, som svetsning eller kallbearbetning.
Scana Booforge har hög och erkänd kompetens på detta område.
– För höghållfasta stål utgör värmebehandlingen ofta hälften av specifikationen, berättar Henrik Fintling. Vi har byggt upp den här avancerade behandlingen till en kundtjänst som nu står för 20 % av vår omsättning.
Åter till vår gaffel, som nu har fått sin slutliga form och styrka. Nu återstår slutbearbetning, anpassningar, påsvetsning av detaljer och omfattande sluttester med ultraljud och magnetpulver, och utfärdande av testcertifikat.
– Vi säljer inte små lagergafflar, nedre gränsen går vid truckar som lyfter 8 ton, den övre vid 150 ton. I det lägre området har vi mycket konkurrens, men när det gäller kraftigare gafflar dominerar vi marknaden.
Det är inte fråga om någon serietillverkning eftersom två gaffelpar sällan är lika. På företaget finns en konstruktör som driver utvecklingsprojekt med kunderna, som ofta är tyngre industri, sågverk, pappersindustri, stålverk och stenbrott.
– Vi samarbetar med Scana Machining i Kristinehamn, förklarar Henrik.
Samarbetet gäller till exempel de långa, smala stålcylindrar som ligger på golvet och påminner om Bofors bakgrund som försvarsindustri. Efter borrning och efterbehandling ska cylindrarna bli eldrör för de kanoner som byggs av BAE Systems Bofors, där numera den verksamheten återfinns.
I Kristinehamn träffar vi Torsten Blomberg, som är VD för både Scana Booforge och Scana Machining. Han konstaterar att Scana Machining ägnar sig åt bearbetning av stora detaljer och att man har en maskinpark därefter. Marknadssegmenten Offshore, Propulsion och Energy har en förkärlek för robusta varor, i form av produkter som rör, förankringar och propelleraxlar.
– Här på Scana Machining gör vi allt som har med färdigberbetning att göra. Vi utför till exempel avancerad svetsning, bland annat gör vi åt försvarsindustrin mycket lätta konstruktioner i olika speciallegeringar, och vi gör också till exempel invändig påläggssvetsning med Inconel för kopplingar inom offshore-sektorn.
Både Booforge och Machining uppfyller standard ISO3834-2, som ställer långtgående krav på svetsverksamheten, till exempel vad gäller utrustning, kontroller, dokument och inköpsförfarande. Även på personalsidan är det väl sörjt med egna svetsspecialister enligt de internationella standarderna IWS och IWE.
Många av de produkter som ligger i fabriken är alltså långa och slanka. När vi kommer på besök pågår en stillsam svarvprocess, när en 12-meters propelleraxel under långsam rotation förses med lagerlägen för stödlagren. Rör för offshoreindustrin och eldrör för kanoner och haubitsar är andra exempel. Gemensamt för alla är strikta krav på materialets egenskaper och precision i tillverkningen.
– Vi kan svarva längder på upp till 22 meter med IT6-tolerans, förklarar Torsten Blomberg. Den här tillverkningen av kräver mycket manuell hantering på grund av materialets längd och fjädrande egenskaper.
Även fräsning av stora detaljer är det sörjt för. Den största fräsmaskinen är en 7-axlig Fermat med rundmatningsbord som kan ta detaljer på 14 meter och upp till 25 ton, och ända upp till 60 ton på det fasta bordet.
Det råder inget tvivel om att Scana Machining har kunder som ställer krav. Det blir inte minst tydligt när man kliver in till Sonia Nauclér, som styr över företagets kalibrering av mätmaskiner, och inte minst över den enorma uppsättning mätdon som finns, från det minsta upp till mikrometrar på 2,5 meter. Här kan man också erbjuda kalibrering av mätutrustning som en tjänst. Ute i fabriken finns bland annat en koordinatmätmaskin som med sitt bord på 4 x 2 x 1,6 meter och en maxlast på 5 ton är den av de största i Sverige av sitt slag.
Innan leverans görs grundliga provningar av produktens egenskaper.
– Sluttesterna utförs inom ramen för begreppet oförstörande provning (non-destructive testing, NDT), och vi har personal som är certifierade för nivå 3, som är den högsta nivån, berättar Torsten Blomberg.
Testerna omfattar UT, MT, PT och OT, uttolkat som ultraljudstest, magnetpulvertest samt penetrerande och optisk test för att kontrollera materialtjocklek och hitta porer, sprickor och andra avvikelser från specifikationen. Produkter som ska driva fartyg, avlossa kanonskott eller i 30 år förankra borrplattformar tusen meter under havsytan får inte ha några brister.